1. Nguồn phát sinh mùi
Trong sản xuất công nghiệp, mùi có thể phát sinh từ nhiều nguồn khác nhau:
- Mùi từ nguyên liệu sản xuất của các ngành chế biến thủy hải sản, cao su, bột tôm, hóa chất…. có nguồn gốc tự nhiên hoặc nhân tạo. Các nguyên liệu bản thân đã có mùi đặc trưng hoặc phát sinh mùi do sự phân hủy các hợp chất hữu cơ trong quá trình vận chuyển, lưu trữ.
- Mùi từ quá trình sản xuất công nghiệp. Trong quá trình sản xuất, mùi hóa chất, phụ phẩm hoặc mùi hữu cơ phát sinh trong công đoạn sấy, chưng cất.
- Mùi sinh ra từ hệ thống xử lý nước thải do bay hơi và lên men sinh học tại khu vực các bể: thu gom, điều hòa, tách dầu mỡ, lắng, xử lý kỵ khí, xử lý hiếu khí và xử lý bùn.
- Thành phần khí ô nhiễm gây mùi thường chứa nhóm các chất gây mùi có khả năng dễ định lượng dưới dạng vô cơ như ammoniac, hydrosulfua… hay nhóm các chất hữu cơ như thuốc bảo vệ thực vật, dung môi hữu cơ (metan, butan, benzen, xylen, xiclohexanon, toluen…) hoặc nhóm các chất rất khó định lượng, bay hơi ở điều kiện nhiệt độ thường như VOC (gồm nhiều chất hữu cơ bay hơi mà điển hình là nhóm các chất thuộc ngành công nghiệp sản xuất thực phẩm (mùi gia vị), mỹ phẩm….
2. Một số giải pháp xử lý mùi
2.1. Xử lý mùi bằng phương pháp hấp thụ:
2.1.1. Hấp thụ bằng natricacbonat

- Hỗn hợp khí thải được đưa vào tháp hấp thụ 1 của hệ thống xử lý, tại đây xảy ra phản ứng: H2S + Na2CO3 → NaHS + NaHCO3.
- Dung dịch bão hòa từ tháp 1 sẽ được dẫn vào tháp 2 và được làm bốc hơi bằng khí nóng trong tháp hấp thụ để thu hồi lại Na2CO3.
- Na2CO3 được thu hồi sẽ được dẫn trở lại tháp 1 và lặp lại chu trình.
- Ở tháp 2 quá trình sấy khô không khí diễn ra và được quạt 3 thổi lên đỉnh tháp, đưa đến công đoạn tiếp theo để thu hồi lưu huỳnh đơn chất và hoàn nguyên vanadat.
- Ưu điểm: Dễ dàng tuần hoàn và thu hồi hóa chất cho quá trình phản ứng nên ít tốn hóa chất.
2.1.2. Xử lý bằng NaOH
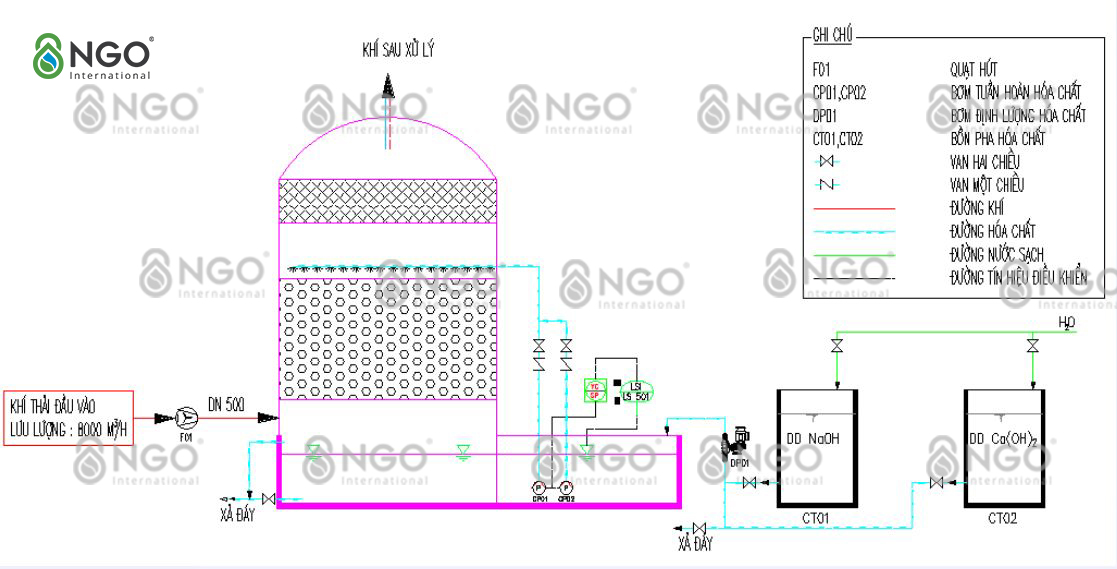
- Khí thải được đưa vào tháp xử lý số 1. Đây là loại tháp đệm với lớp đệm là các khâu sứ Raschig.
- Khí H2S được dẫn vào ở đáy tháp và khí sạch sau khi hấp thụ được đi ra ở đỉnh tháp. Dung dịch hấp thụ được phân phối đều lên lớp đệm và chạy dọc theo bề mặt vật liệu. Phản ứng hấp thụ được diễn ra trên bề mặt ướt của lớp vật liệu đệm.
- Dung dịch đã hấp thụ được đưa vào thúng chứa dung dịch đã dùng số 2.
- Một phần dung dịch ở thùng số 2 được trộn với dung dịc xút mới ở thùng số 4 và hoàn lưu lại tháp vào tháp nhờ bơm 6 để tiếp tục chu trình mới.
- Phần còn lại của dung dịch số 2 được đưa qua thùng xử lý vôi clorua (thùng 3) trước khi thải ra môi trường.
- Nồng độ chất kiềm trong dd hấp thụ không chế ở mức 7 g/l.
- Vận tốc khí trong tháp là 0,6 m/s.
- Lượng NaOH tiêu hao quy về lượng lưu huỳnh là 8 kg.
- Có thể thay NaOH bằng CaCO3.
- Ưu điểm:
+ Đảm bảo xử lý 100 % H2S trong khí thải.
+ HTXL không đòi hỏi phải làm bằng vật liệu chống axit.
+ Thiết bị rửa khí có lớp đệm còn có khả năng hạ nhiệt độ và lọc bụi ướt có trong khí thải.
- Nhược điểm:
+ Khó khăn trong khâu vệ sinh vật liệu đệm.
+ Dễ gây tắc nghẽn vật liệu đệm do quá trình tích tụ cặn.
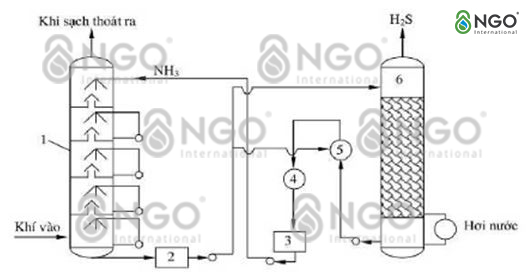
Sơ đồ công nghệ
2.1.3. Xử lý bằng NH3
- Khí H2S được đưa vào đáy tháp hấp thụ dạng mâm chóp, dung dịch hấp thụ NH3 được chảy tràn từ trên xuống xuyên qua các mâm chóp , tiếp xúc pha với dòng khí đi lên, tại đây xảy ra quá trình hấp thụ. Khí sạch được đưa ra ngoài tháp.
- Dung dịch được hấp thụ đi qua bình chứa số 2 và thấp cất khí số 6, (NH4)2S phân giải thành NH3 và H2S ở môi trường nhiệt độ và áp suất thích hợp. Tại tháp xảy ra quá trình chưng cất bằng hơi nước để tách H2S ra khỏi dung dịch và đưa ra ngoài, phần NH3 còn lại được đưa qua các thiết bị làm nguội trước khi hoàn lưu lại tháp hấp thụ.
- H2S tiếp tục được đưa qua công đoạn điều chế axit hoặc lưu huỳnh đơn chất.
- Ưu điểm:
+ Quá trình xử lý tuần hoàn được 100 % dd hấp thụ.
+ Quá trình đơn giản, được áp dụng rộng rãi.
+ Nguyên liệu dễ kiếm, giá thành rẻ.
- Nhược điểm:
+ Tốn thời gian hạ nhiệt cho qua trình giải hấp.
+ Có mùi hôi, khai
2.2. Xử lý mùi bằng phương pháp hấp phụ
2.2.1. Hấp phụ bằng oxit sắt
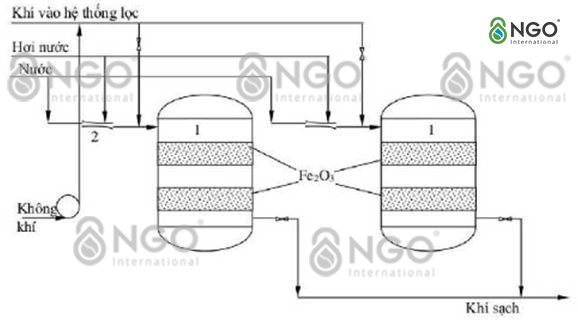
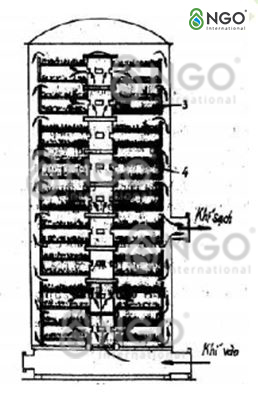
- Đối với hệ thống lọc đơn giản lắp song song:
+ Gồm nhiều bình lọc lắp song song theo chiều đi của khí, mỗi bình có nhiều lớp vật liệu hấp phụ để khí đi qua hết lớp này đến lớp khác. Mỗi lớp vật liệu dầy khoảng 0,3 – 0,5 m. Hệ thống van khí trên đường ống cho phép cắt bất kỳ bình hấp phụ nào đã bão hòa để hoàn nguyên. Nếu bình hấp phụ có 4 lớp thì hiệu quả là 99-99.9 %.
+ Khí thải chứa H2S sẽ theo hệ thống dẫn khí đi vào bên trong các bình lọc, sau đó được giữ lại ở vật liệu lọc theo phản ứng: Fe2O3 + 3H2S → Fe2S3 + 3H2O. Sau đó khí sạch được đưa ra ngoài.
+ Phản ứng trên xảy ra đến khi lớp vật liệu lọc được bão hòa thì hệ thống dẫn khí sẽ ngắt để hoàn nguyên theo phản ứng: 2Fe2S3 + 3O2 → 2Fe2O3 + 6S. Lớp vật liệu lọc sẽ được thay thế và tiếp tục xử lý.
+ Lớp vật liệu hấp phụ được coi là hết tác dụng khi S chiếm 50% lượng vật liệu.
- Đối với hệ thống tháp hấp thụ: Hoạt động đơn giản như bình lọc đơn giản, nhưng khi hoàn nguyên sẽ thổi chung oxy vào để xử lý hoàn nguyên song song.
- Ưu điểm:
+ Quy trinh đơn giản, dễ thực hiện.
+ Hiệu suất rất cao, >90%.
+ Vật liệu rẻ tiền.
- Nhược điểm: Mất thời gian để thay vật liệu lọc
2.2.2. Hấp phụ bằng than hoạt tính
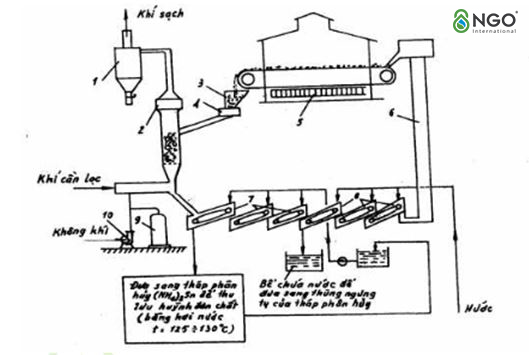
- Khí cần lọc được quạt cấp không khí thổi vào tháp hấp phụ 2, ở đây xảy ra quá trình oxy hóa H2S trên bề mặt than hoạt tính.
- Lưu huỳnh được giải phóng ra trong phản ứng dần dần tích tụ trên bề mặt than hoạt tính. Khí được xử lý đưa qua Cyclon 1 để lọc bụi và vật liệu hấp phụ và đưa qua các công đoạn xử lý tiếp theo.
- Sau khi vật lliệu hấp phụ trở nên bão hòa có chứa S thì được tiến hành hoàn nguyên vật liệu hấp phụ bằng (NH4)2S được đưa vào tháp phân hủy 7 để thu S đơn chất.
- Lưu huỳnh được thu nhờ sự khác nhau khối lượng đơn vị, còn hơi ngưng tụ lại trong quá trình ngưng tụ là (NH4)2S
- Sau khi tách S ra khỏi than bão hòa, người ta rửa than bằng nước cho tới khi không còn SO2 trong nước mới thôi. Sau đó than được sấy khô để dụng trở lại.
- Than được vận chuyển bằng gầu nâng 6, đến nhà sấy băng tải 5, qua phễu rót 3 đưa vào tháp hấp phụ 2 để tiếp tục quá trình. Việc điều chỉnh lưu lượng than trước khi đưa vào tháp nhờ vào thiết bị khống chế lưu lượng 4.
- Ưu điểm:
+ Quy trình đơn giản, dễ thực hiện/
+ Hiệu suất cao, >90%.
+ Độ tinh khiết của lưu huỳnh cao: 99.9%
- Nhược điểm: Khí thảo cần phải lọc bụi trước khi đưa vào hệ thống hấp phụ ( nồng độ bụi 2-3 mg/m3)
***Vui lòng đọc kỹ yêu cầu về Điều khoản sử dụng – Bản quyền trước khi sao chép hoặc trích dẫn nội dung và hình ảnh của website.
Trang web này thuộc bản quyền của Công ty TNHH Quốc tế NGO (NGO International). Bất kỳ hình thức sử dụng hoặc sao chép một phần hoặc toàn bộ nội dung dưới mọi hình thức đều bị nghiêm cấm, trừ trường hợp được sự cho phép rõ ràng bằng văn bản từ Chúng tôi.