TEXTILE DYEING WASTEWATER TREATMENT
1. Textile dyeing wastewater wastewater composition
The textile dyeing industry currently plays an important role in Vietnam's economy. Besides its great contributions to the country's development, the textile dyeing industry also brings many negative impacts on the environment, especially wastewater from the production process. Every year, the textile industry in general and the textile dyeing industry in particular are discharging a large amount of wastewater into the environment with high concentrations of pollution because it has not been treated or has been treated but does not meet allowed standards.
Among the main stages of the textile industry, the dyeing and finishing stages often generate the most wastewater. The wastewater composition is unstable and varies according to the type of dyeing equipment, dyeing materials, and chemicals. Textile dyeing wastewater usually includes three main groups of chemicals: (1) The dye group includes direct, disperse, reactive, acidic dyes containing chromium metal, vat and sulfur; (2) additives include mordants and fixatives, often heavy metal salts; (3) Other chemicals include acids, inorganic salts, caustic soda and oxidants, starch, etc…
Basically, textile dyeing wastewater often has high temperature, color, PH, BOD and COD. On the other hand, wastewater from the textile dyeing industry contains a number of chemicals with heavy metals and toxic ingredients that can not only kill aquatic life but also directly affect the human life.
Criteria |
Unit |
Concentration |
PH |
- |
8,6 – 9,8 |
Temperature |
°C |
36 – 52 |
Color |
Pt-Co |
350 – 3710 |
COD |
mg/l |
360 – 2448 |
BOD5 |
mg/l |
200 – 1450 |
2. Current status of textile dyeing wastewater treatment technology
Some technologies applied at textile and dyeing enterprises in the wastewater treatment process include: (1) physicochemical combination (flocculation) and filtration; (2) combine physicochemistry and aerobic biology or vice versa; (3) combining physicochemistry, aerobic biology and physicochemistry; (4) combine physiccochemistry, biology and filtration (sand or activated carbon filtration).
Due to the specific characteristics of the textile dyeing industry, which uses temperature during the dyeing process, wastewater often has high temperatures. In the production lines of some textile and dyeing enterprises, cooling towers or cooling rigs are often used to reduce the temperature of wastewater before collecting it in the treatment system. In general, the traditional technologies currently applied in the treatment of textile and dyeing wastewater still have many shortcomings and are not very effective due to the complex treatment process and space-consuming treatment of pollutants, especially COD, color level to unstable output water quality...
3. Effective textile dyeing wastewater treatment technology using MBR-X technology
The nature of MBR-X technology is to operate with low membrane pressure when placing the MBR-X module underwater. When the module operates, water penetrates through the film and through the water distribution holes to flow into the pipes, from which it flows out into 2 water channels along the sides. The special flow path structure of the MBR-X module helps water penetrate the membrane quickly, reducing resistance to a minimum and keeping pressure across the membrane when the module operates at low conductivity levels. With its innovative design, MBR-X allows the flow to expand gradually, reducing losses to low levels and operating at lower membrane pressures. MBR-X rarely causes membrane clogging, helping to maintain stable filtration performance.
Currently, MBR-X technology is applied to the projects with different discharge capacities from 20 m3/day and night or more and applied to many business lines. In particular, this technology has been applied to treat textile dyeing wastewater at Hangzhou Zhongqiang Print & Dye Co. Ltd (Hangzhou, China), discharge capacity of 3,000 m3/day, installed area of MBR-X membrane tank is 120 m2 (need about 40 MBR-X200 modules), total system installation area is 843 m2 , operating costs equivalent to 11,823 VND/m3 of wastewater, reusing 80% of treated wastewater.
MBR-X technology can be effectively combined with other technologies such as anaerobic, aerobic, SBR or AB and combines the advantages of hollow membranes and flat sheet membranes; no pump required, patented flow distribution design; Saves electricity costs during operation and can extend the life of the biological membrane. And also, MBR-X saves space, increases microbial density by 3-4 times, water retention time is only 4 hours and reduces operating costs of the wastewater treatment system. This is an effective technology for the enterprises that are looking for solutions to replace physical and chemical technology and want to apply membrane technology and biotechnology in wastewater treatment to reuse water sources.
Textile dyeing wastewater after treatment at the MBR-X system is guaranteed to meet column A or column B standards according to QCVN 13-MT: 2015/BTNMT.
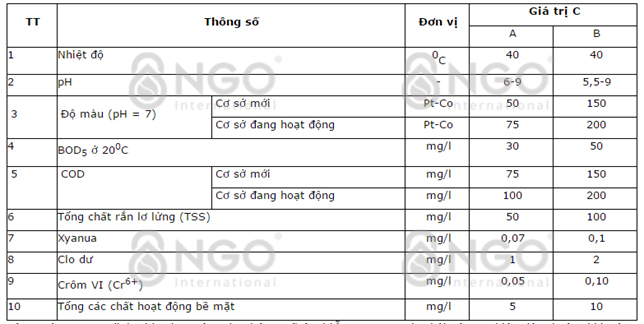
References:
MSc. Nguyen Thanh Ngan (Vietnam Textile and Garment Group) – Effectiveness of wastewater treatment using microbiological technology
http://tapchimoitruong.vn/pages/Hiệu-quả-xử-lý-nước-thải-bằng--công-nghệ-vi-sinh
***Vui lòng đọc kỹ yêu cầu về Điều khoản sử dụng – Bản quyền trước khi sao chép hoặc trích dẫn nội dung và hình ảnh của website.
Trang web này thuộc bản quyền của Công ty TNHH Quốc tế NGO (NGO International). Bất kỳ hình thức sử dụng hoặc sao chép một phần hoặc toàn bộ nội dung dưới mọi hình thức đều bị nghiêm cấm, trừ trường hợp được sự cho phép rõ ràng bằng văn bản từ Chúng tôi.